Pitting and Crevice corrosion of 904L/EN 1.4539/UNS N08904 material
Chloride ions in a neutral or acidic environment facilitate local breakdown of the passive layer. As a result, pitting and crevice corrosion of 904L/EN 1.4539/UNS N08904 material can propagate at a high rate, causing corrosion failure in a short time. Since the attack is small and may be covered by corrosion products or hidden in a crevice, it often remains undiscovered until perforation or leakage occurs.
Resistance to pitting corrosion is determined mainly by the content of chromium, molybdenum and nitrogen in the stainless steel. This is often illustrated using the pitting resistance equivalent (PRE) for the material, which can be calculated using the formula: PRE = %Cr + 3.3 x %Mo + 16 x %N. The PRE value can be used for rough comparisons of different materials. A more reliable means, however, is to rank the steel according to the critical pitting temperature (CPT) of the material. There are several different methods available, for example ASTM G 150 that uses the Avesta Cell with a 1M NaCl solution (35 000 ppm or mg/l chloride ions). The CPT-values are shown in the table below. Higher contents of chromium, molybdenum and nitrogen also enhance the crevice corrosion resistance of the stainless steel.
Both ASTM G150 and G48 are methods for ranking the relative pitting or crevice corrosion resistance for the different stainless steels but they do not give the maximum temperature for using these alloys in real service environments.
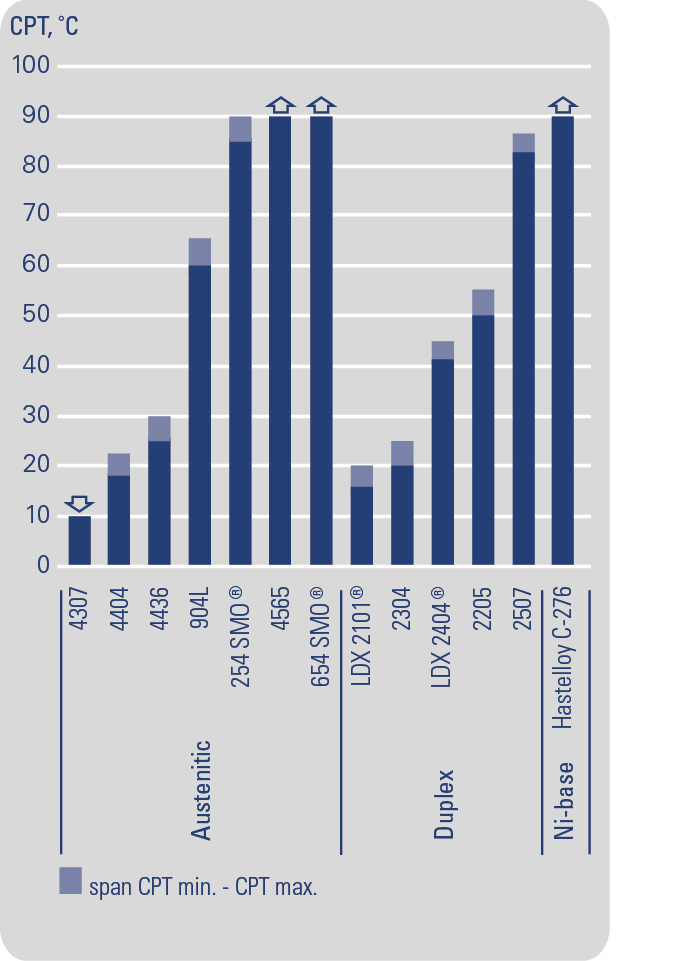
Welding of 904L/EN 1.4539/UNS N08904 material
All the highly alloyed austenitic steels are well suited for welding and the methods used for welding conventional austenitic steels can also be used on 904L/EN 1.4539/UNS N08904 material. However, due to the stable austenitic structure, it is somewhat more sensitive to hot cracking in connection with welding and generally welding should be performed using a low heat input. On delivery, sheet, plate and other processed products have a homogeneous austenitic structure with an even distribution of alloying elements in the material. Solidification after partial remelting, e.g. by welding, causes redistribution of certain elements such as molybdenum, chromium and nickel. These variations, segregation, remain in the cast structure of the weld and can impair the material’s corrosion resistance in certain environments. The welding wire style of 904L/EN 1.4539/UNS N08904 material is ER385 and the electrode is E385.
|